Process Solutions recently completed a project for a small potato chip company that entailed the commissioning of new batch fryers coupled with the design, build and commissioning of a modern control system.
This regional potato chip company serves the Western Michigan market with artisanal, hand seasoned potato chip products. Up until now, the customer was using an antiquated frying system with low production output. However, upon experiencing rapid sales growth and increasing demand for their products, the customer realized they needed a new fryer system with modern controls to increase their production output and expand their business.
To achieve a higher production output, Process Solutions commissioned 2 new Batch Fryer provided by a partner company to replace the existing antiquated fryer. In addition, Process Solutions designed, built, and commissioned a new control system, which included a CompactLogix PLC with 96 I/O points, a 10” door mounted touch screen HMI, seven PowerFlex 525 drives, and all the necessary system software.
To complete this project, Process Solutions deployed an experienced team of software and controls engineers. Travis, the software engineer assigned to the job, has been with Process Solutions for 2 years and was responsible for all in office software development. With the completion of the project, Travis’s software package effectively operated all system timers, connected motors, and sensor inputs – “we design our software to be the brains of the system” explained Travis, “our goal is to allow the operator to be as hands-off as possible so they can instead focus on higher impact tasks on the production line.”
Mark, who has been a Process Solutions Project Engineer for more than 13 years, was also assigned to the project. Mark’s responsibilities included commissioning the new Batch Fryer and control equipment, as well as the start-up of the production line.
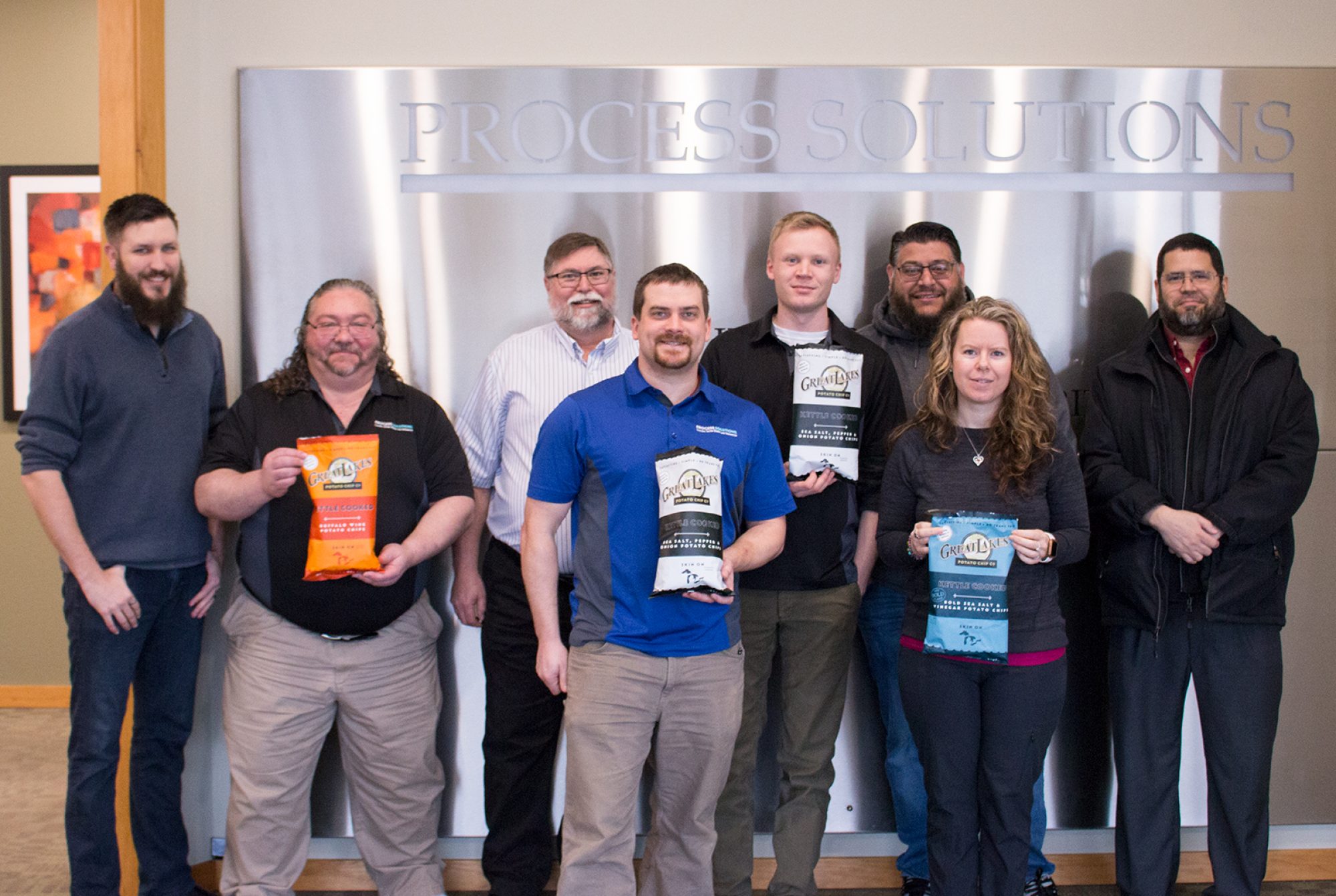
Upon completion, Mark noted that one of the most challenging aspects of the project was integrating the facility’s existing control technology with the modern technology that Process Solutions was installing. Despite the challenges, Mark successfully completed the project on time and within the allotted budget. According to Mark, “after the project was complete, the customer expressed to me that he was extremely impressed with how well Process Solutions worked as a group and the sense of urgency that we displayed. They seemed very pleased with how quickly we responded to their requests.”
With the installation and commissioning of the new Batch Fryer and the corresponding control system, the potato chip company is now achieving a production output of roughly 600lbs of potato chips an hour.
With over 30 years in business, Process Solutions has emerged as an industry leader in control system design and integration. Quality and experience are built into every control system that ships from Process Solutions’ 30,000 sq. ft. facility in Stanwood, Washington. For more information, please visit www.processsolutions.com